If you’re interested in a career in the oil and gas industry, supplementing an engineering design technology diploma with knowledge of process piping systems is a great way to bring specific expertise to the field. Process piping systems are utilized to convert raw materials such as fuels and gases into functional products. Process piping systems consist of a particular order of interconnected pipes, valves, tubing, pressure vessels, separators, strainers, gaskets and other components. All of these work together to transport chemical compounds, gases and other fluids from their source to their final destination.
Process piping experts utilize their knowledge of engineering design technology to come up with designs for process piping systems, which can be used at sites such as petroleum refineries while keeping in line with industry regulations and codes. If you’re interested in the design of process piping, it’s important to familiarize yourself with the steel types most frequently used in its construction.
Steel as the Material of Choice
Steel is the most commonly used material for process piping drafting. Steel’s general durability, including its ability to withstand high temperatures and corrosion, makes it a great choice in the manufacturing of process piping, especially in facilities such as petroleum refineries in which piping systems are used to transport toxic and harmful materials.
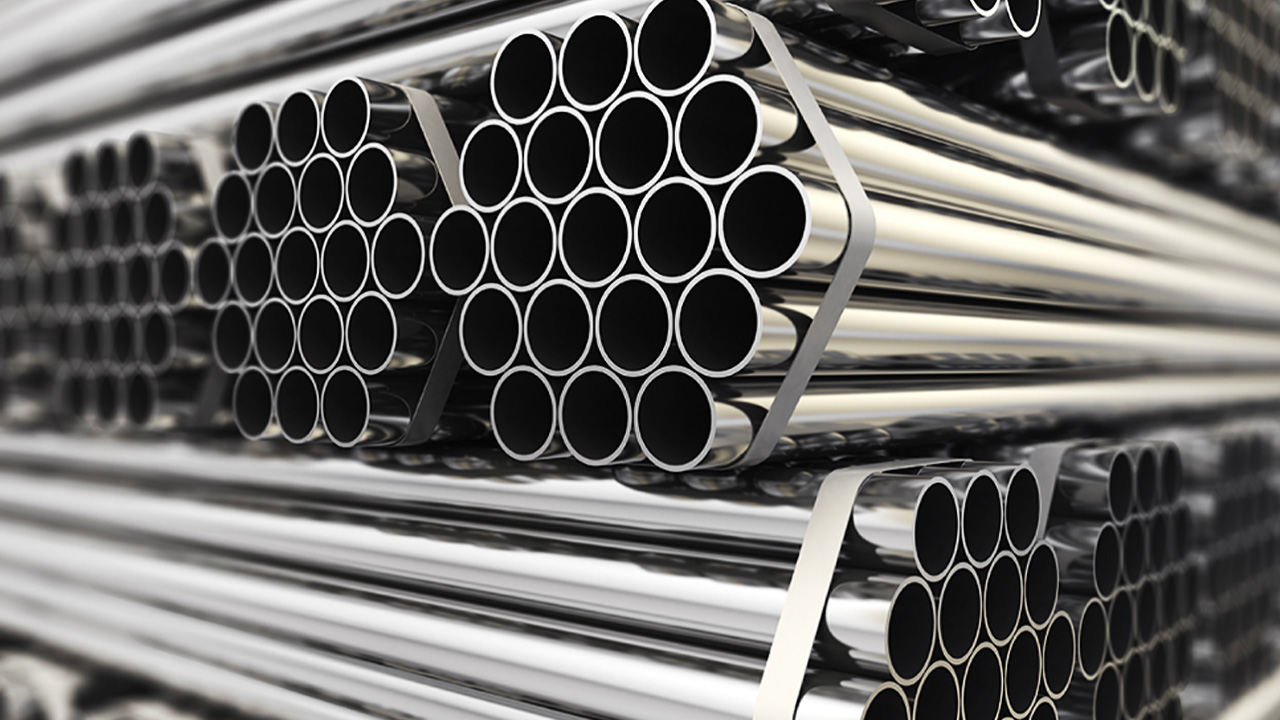
Steel is the most common material for use in process piping drafting due to its durability and resistance to corrosion
A wide range of grades and qualities make steel a good choice for the transportation of a number of different grades and materials. At its most basic level, steel is an alloy of iron and carbon and is occasionally composed of additional metals such as cobalt, tungsten, chromium, nickel, and aluminum. Of its many different grades and qualities, steel can be categorized into four different types according to chemical composition. These types include carbon steel, stainless steel, alloy steel, and tool steel, all of which have different advantages in terms of their use for process piping systems.
Carbon Steel: The Most Frequently Used Steel Type
Carbon steel is the most frequently used steel material in the process piping industry, preferred for use in the chemical industry, general refinery factories, and process plants. Carbon steel is set apart by its durability, toughness, flexibility and malleability. Carbon steel contains only a small amount of allowing elements in scant concentrations, making it generally inexpensive for use.
Carbon steel has a working temperature range of -29℃ up to 427℃, and certain low-temperature carbon steel may be used at temperatures as low as -46℃. While carbon steel is durable, if you’re getting your process piping diploma, it’s important to note that its lack of alloying elements makes this type unsuitable for extreme temperatures or high pressure, as it is not as resistant as other types of steel.
Stainless Steel Provides Protection Against Corrosion
Stainless steel is best known for its rust-resistant qualities. It is also valuable for piping systems needed to transport highly corrosive materials, as stainless steel is not susceptible to corrosion. Stainless steel’s primary alloy is typically chromium, with other alloys including nickel, silicon, molybdenum and manganese. When exposed to oxygen in air and water, the alloys in stainless steel form a film over the material which prevents against corrosion.
Stainless steel has a range of working temperatures, from -257℃ up to 538℃, and includes three different groups defined by their crystalline structure. Martensitic stainless steel is composed of around 11-17% chromium, around 1.2% carbon, and less than 0.4% nickel. This steel is ideal for surgical equipment, knives and other cutting tools due to its heat-treatable and magnetic qualities. Ferritic stainless steel contains more chromium (15%-30%) and has a low carbon content of 0.1%, making it more resistant to corrosion and scaling. Austenitic stainless steels are the most corrosion-resistant of the three, making these the favored choice in the piping industry. Austenitic steels contain 16-26% of chromium and low carbon content of 0.08%.
Alloy Steel Has Multiple Uses
Alloy steel refers to a number of different types of steel composed of specific combinations of alloys in varying concentrations. Different alloying elements give steel different properties such as corrosion resistance, malleability, strength, or weldability, and certain combinations are preferred for specific uses. Chromium and silicon elements can give steel improved hardness, corrosion resistance and abrasion, while molybdenum allows for extreme heat resistance. Nickel increases steel’s resistance at low temperatures, as well as its toughness.
For piping systems put into place in extremely hot or cold conditions, high alloy steel is preferred, as its increased alloy count makes it more durable.
Tool Steel: Not Ideal for Process Piping
Tool steels are characterized by a much higher quantity of alloys, including vanadium, molybdenum, tungsten, and cobalt, making them ideal for withstanding exposure to extremely high temperatures. However, those with process piping training should know that tool steel’s higher alloy count makes it an unpopular choice for piping materials, as these are typically formed with softer steels. Tool steel is expensive to manufacture, and its strength makes the formation of piping materials difficult. Tool steels are best suited for drilling and cutting equipment due to their durability.