Oil and gas products often need to be kept cool, and so heat exchangers are sometimes used to ensure a balanced heat level in pipelines and process plants. Depending on the project, these can take different forms.
Students who decide to complete Engineering CAD Technician training with a Process Piping Specialization learn about heat exchangers in their Process Plant Equipment Drawings and Theory course. To help them prepare for their future career, students learn how these components are maintained, designed, and installed.
Want an advance look at some of the different kinds of heat exchangers that CAD professionals could help create? Here are a few that you might encounter after your training.
1. Shell & Tube Exchangers Are Sometimes Seen by Pros With BIM Training
A very common type of heat exchanger used in the petroleum industry is the “shell & tube.” This technology works by putting one liquid or gas in the shell, and then another liquid or gas in a series of tubes running through the shell. The tubes’ contents will increase or decrease the temperature of the shell’s contents, depending on what’s needed. This design is also common for projects like building heating, and other industries that require efficient temperature regulation. Given the prevalence of this design, odds are good that you will encounter it if you work in designing process plant equipment after completing your BIM training.
2. Spiral Heat Exchangers Offer Effective Exchange in a Small Package
While light crude oil tends to be quite fluid, intermediate and heavy crude, and some other petroleum products, can be quite vicious. For projects where space is limited or processed fluids are quite viscous, a “spiral heat exchanger” may be best. Spiral exchangers feature two tubes wrapped together in a fairly tight spiral. A hot liquid flows in one direction, and a cool liquid flows in the other. This has the effect of moving both temperatures closer to a midpoint and allows the exchange to take place in quite a small space.
If you work in process piping drafting and are called on to design a heat exchanger for a plant dedicated to this kind of product, a spiral heat exchanger could be the best fit.
3. Pros With BIM Training Can Save Resources With Air-Cooled Heat Exchangers
A downside of many types of heat exchangers is that they require quite a lot of water to be effective. To reduce resource usage, professionals sometimes opt for an air-cooled heat exchanger instead. This type of heat exchanger uses a fan to blow cool air across a series of finned tubes, which carry the liquid that is in need of cooling.
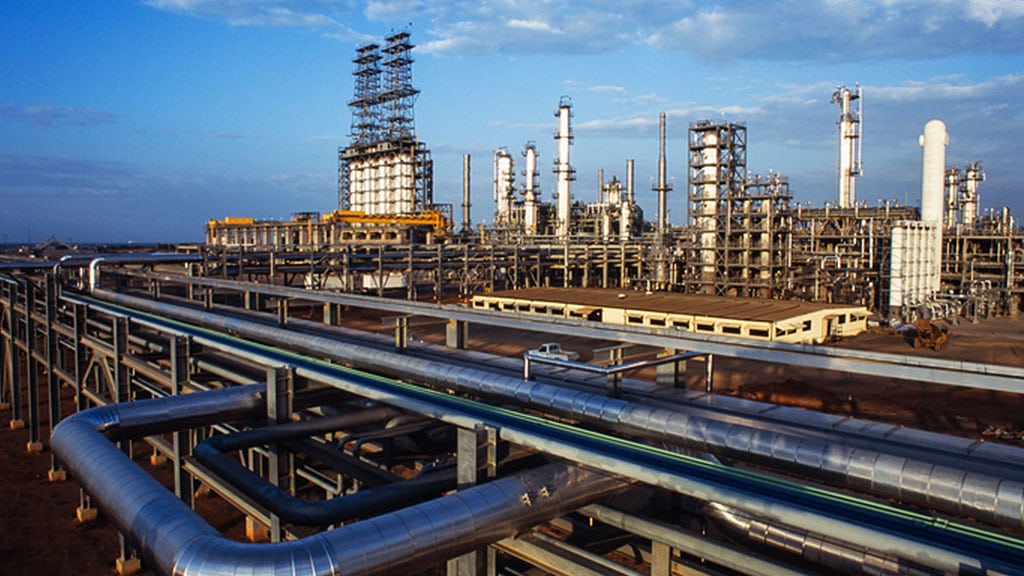
Air-cooled heat exchangers let plants operate with less water
Because efficiency in the transfer of air is required for this to work well, it’s important that there are few obstructions—in the form of other structures or equipment—in the way of the fan and the tubes in need of cooling. If ever you are tasked with modeling an air-cooled heat exchanger in your future career, you’ll want to make sure that fans are free and clear to cool the liquids in the pipes.
Do you want to become an engineering CAD technician with a specialization in Process Piping?
Visit Digital School to learn more about our training program!